由于超级双相不锈钢含氮量高且高温下易析出影响材料性能的金属间相,因此常规生产大型超级双相不锈钢铸件主要是先经过冶炼及精炼技术制成钢坯,再进行压力加工或焊接制备出相关零件(俗称两步法)。本项目是在原有中频感应炉的基础上直接增氮,通过设定新的高铬高氮材料成份以及新的熔炼与精炼工艺来解决高含氮量与无气孔缺陷之间的矛盾;采用特殊砂型铸造工艺解决了超级双相不锈钢在大型铸件生产中容易出现裂纹等问题,以一步法生产出大型无铸造缺陷铸件。同时,研究发现高氮量能促进铬元素在两相中均匀分布以及提高材料力学性能和耐蚀性能,免除了常规固溶处理工艺,起到节能减排、降低成本和提高经济效益的作用。
技术指标:本项目技术开发的产品与美国标准ASTM A890 超级双相不锈钢(锻件)性能对比数据见表1 所示。
表1 两种产品性能对比
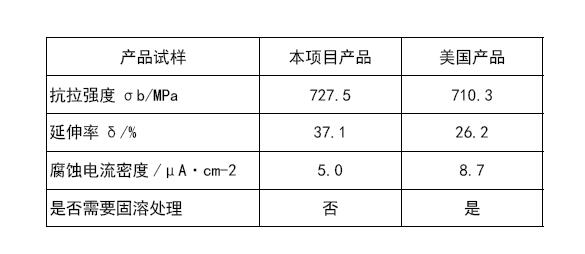
由表1 可看出,本项目开发产品具有比美国产品更优异的力学性能和耐蚀性能,且不需要固溶处理,节能减排效果显著,同时降低了生产成本,缩短了生产周期。经济效益及应用推广情况:本项目在不改变原有熔炼设备的情况下,以氮代镍并利用高氮表现出有利材料性能原理,采用循环脱氧以及特殊铸造成形工艺,实现“一步法”生产超级双相不锈钢铸件,并且免除了传统意义上的固溶处理,节约了成本、提高生产效率和附加值,达到了节能减排的作用;同时该项成果便于在普通企业中推广,扩大双相不锈钢的应用范围。利用本成果能生产结构复杂的大中型铸件,作为海洋石油、核能、造船及化工等行业中的重要关键零部件。